The Future of Manufacturing: Rapid Prototyping CNC
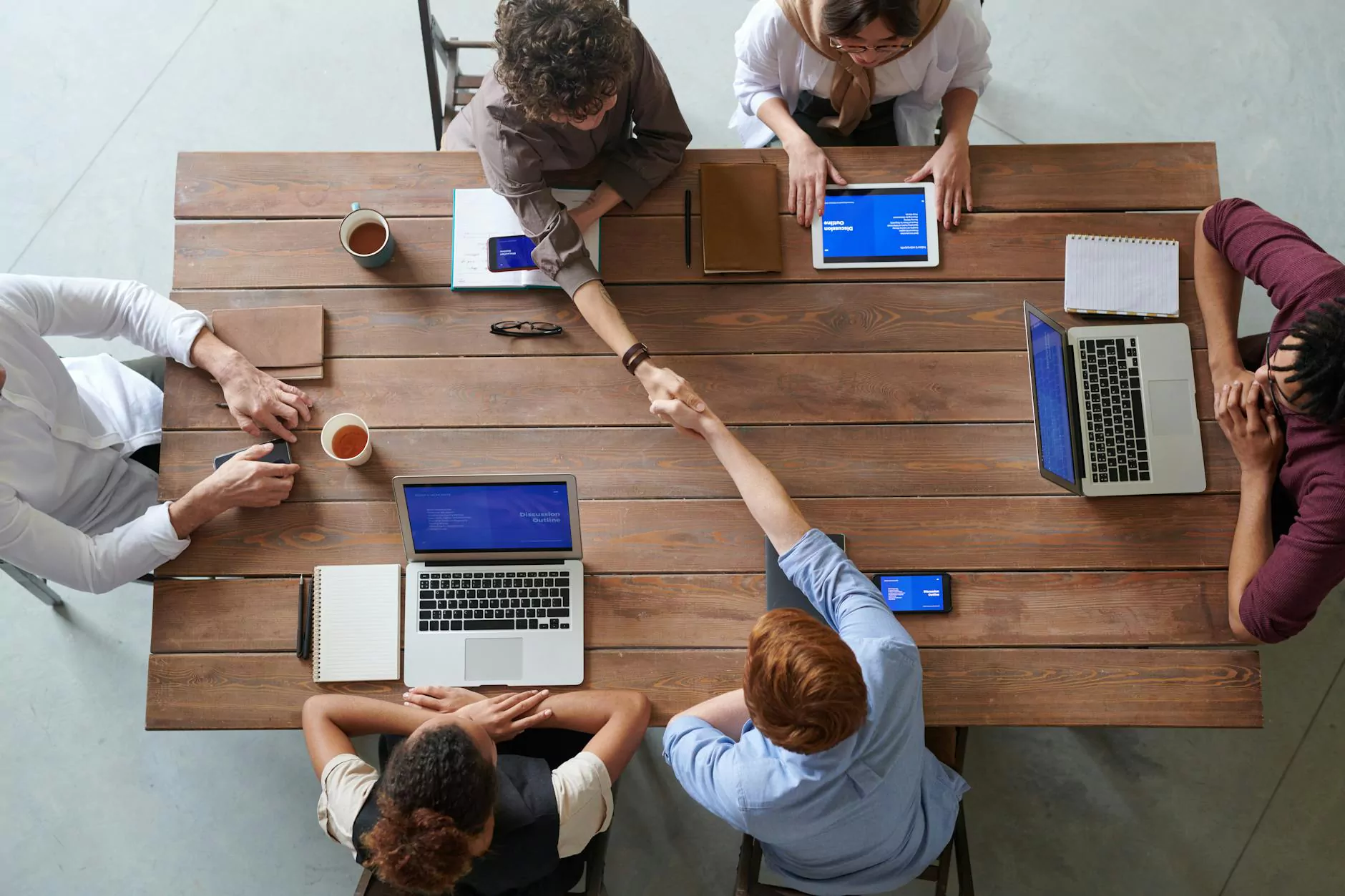
In a world where innovation and efficiency drive success, the manufacturing industry is undergoing a significant transformation. Among the most impactful developments is the rise of rapid prototyping CNC (Computer Numerical Control). This technology has redefined how products are designed and produced, enabling metal fabricators to bring their ideas to life faster and with unparalleled precision. In this comprehensive article, we will delve into the intricacies of rapid prototyping CNC, its benefits, and its role in the future of manufacturing.
Understanding Rapid Prototyping CNC
At its core, rapid prototyping CNC is a method that utilizes computer-controlled machines to create prototypes quickly and accurately. This process typically involves several key stages:
- Design Creation: Utilizing CAD (Computer-Aided Design) software, engineers create intricate 3D models of the product they intend to manufacture.
- Material Selection: Depending on the functionality and design requirements, appropriate materials such as metals, plastics, or composites are chosen for the prototype.
- CNC Machining: The selected material is precisely shaped and formed using CNC machines that are programmed to execute a series of complex movements.
- Finishing Touches: After the initial prototype is crafted, additional processes such as sanding, painting, or polishing are performed to achieve the desired finish.
The Advantages of Rapid Prototyping CNC for Metal Fabricators
Metal fabricators are increasingly adopting rapid prototyping CNC for its numerous advantages. Some of the most prominent benefits include:
1. Enhanced Precision
One of the most significant advantages of using CNC technology in rapid prototyping is the precision it offers. Traditional manufacturing methods can often result in inconsistencies and errors. CNC machines, on the other hand, operate with exceptional accuracy, ensuring that every prototype is made to exact specifications. This is crucial for metal fabricators who require meticulous dimensions, especially in industries like aerospace and automotive, where tolerances can be incredibly tight.
2. Reduced Lead Times
The term “rapid” in rapid prototyping CNC is essential. This technology dramatically reduces lead times compared to conventional manufacturing processes. With CNC machined prototypes, metal fabricators can complete their projects faster, allowing for quicker iterations, testing, and feedback cycles. Such efficiency is vital for staying competitive in today's fast-paced market.
3. Cost-Effectiveness
While the initial setup of CNC machines may seem high, the long-term savings are undeniable. Rapid prototyping CNC minimizes the wastage of materials, and since iterations can be made quickly and easily, businesses can avoid the costs associated with traditional prototyping methods. In essence, this technology allows metal fabricators to produce high-quality prototypes without breaking the bank.
4. Design Flexibility
The capacity for design flexibility provided by CNC rapid prototyping is remarkable. Fabricators can experiment with complex designs that were previously challenging to implement. Changes to designs can be executed swiftly since CNC programming allows for easy modifications without significant downtime.
Applications of Rapid Prototyping CNC in Various Industries
Rapid prototyping CNC spans multiple industries, each benefitting from the efficiency and precision that it provides. Below are a few notable applications:
Aerospace
The aerospace industry demands unparalleled precision and quality, making rapid prototyping CNC an invaluable asset. Complex components, such as turbine blades and structural parts, can be fabricated to the exact specifications required for safety and performance.
Automotive
In the automotive sector, rapid prototyping CNC is used to create intricate parts and assemblies that enhance vehicle performance. From custom tooling to production parts, this technology allows manufacturers to innovate rapidly, respond to market demands, and deliver superior end products.
Medical Devices
The medical field is witnessing significant advancements with the help of rapid prototyping CNC. Customized devices, implants, and surgical tools can be produced quickly and tailored to meet specific patient needs, thereby improving healthcare outcomes.
Challenges in Rapid Prototyping CNC
Despite its many advantages, rapid prototyping CNC does have its challenges. Understanding these obstacles is crucial for metal fabricators to maximize the effectiveness of this technology:
1. High Initial Investment
Investing in CNC machines and CAD software can be costly, and smaller operations might find this difficult to accommodate within their budgets. However, many businesses view this as a long-term investment due to the operational efficiencies gained over time.
2. Skill Requirement
Programming CNC machines and utilizing CAD software requires a certain level of expertise. It is essential for businesses to invest in training their workforce to fully leverage the potential of rapid prototyping CNC.
3. Material Limitations
While rapid prototyping CNC works effectively with many materials, some unique or highly specialized materials may not yield the desired results. It's imperative for metal fabricators to understand the characteristics of the materials they are working with to ensure success.
Best Practices for Implementing Rapid Prototyping CNC
To harness the full potential of rapid prototyping CNC, metal fabricators should consider the following best practices:
1. Thorough Planning
Before commencing any project, it is crucial to have a clear and detailed plan. This includes defining the project scope, understanding material properties, and establishing timelines. A thorough plan can help mitigate challenges during the production phase.
2. Continuous Iteration
Rapid prototyping is fundamentally about quick iterations. Embracing a culture of continuous improvement, where feedback is actively sought and implemented, can lead to innovative designs and heightened product quality.
3. Investment in Training
As mentioned earlier, the skillset required to utilize CNC technology effectively cannot be understated. Regular training and workshops can keep staff updated on the latest developments in CNC technology and enhance their problem-solving capabilities.
Conclusion: The Evolution of Rapid Prototyping CNC
The adoption of rapid prototyping CNC represents a pivotal shift in the landscape of modern manufacturing. For metal fabricators, the ability to produce high-quality, precise prototypes in reduced timeframes stands to revolutionize their operational capabilities. The continued advancements in CNC technology promise an exciting future, with the potential to unlock even greater efficiencies and innovations across various industries.
As businesses adapt to the fast-paced demands of the market, those that leverage rapid prototyping CNC will undoubtedly find themselves at the forefront of manufacturing. By embracing this cutting-edge technology, metal fabricators can ensure they not only meet the current needs of their clients but also pave the way for future advancements in the industry.
Visit deepmould.net to learn more about how rapid prototyping CNC can transform your manufacturing processes and keep your business at the cutting edge of innovation.